Using Aluminium for Tavrida Reclosers Improve Fixed Cost, Handling Procedures, Logistic and Carbon Footprint Of Utility Operation
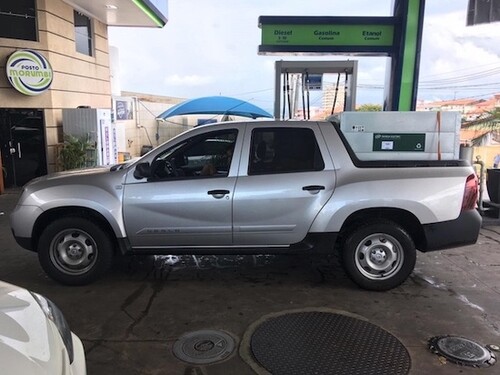
Aluminum is a core material of Tavrida Electric enclosures for outdoor circuit reclosers product line. Apart of obvious advantages such as outstanding mechanical strength and corrosion restraint, this material can provide disparate benefits for Utility fixed cost and carbon footprint decreasing.
Table of Contents- Lightweight Tavrida Reclosers - Convenience in Transportation and Handling
- Using Aluminium VC Stainless Steel in Circuit Reclosers Manufacturing Process
- CF Calculation for Transportation of Outdoor Switching Module and Recloser by Truck
Lightweight Tavrida Reclosers - Convenience in Transportation and Handling
Recloser and package design allow equipment transportation by double-cabin civil pickup and handling of 2 persons without using forklift for loading and unloading! Lightweight module-based design allows individual removing and easy installation any of the recloser components on pallet multiple times. It ensures that no additional packaging materials and related cost and waste disposal pollution will be generated in the process of recloser handling by the Utility and recloser can be delivered on site of installation using the same packaging materials as it was received from manufacturer. Tavrida Electric RC5 recloser control provides huge free space for additional equipment installation and designed to allow handling by one person without lifting crane. Assembled recloser control weight is only 45 kg (can be even 35 kg the battery type and capacity selected) which according to standard NR17 (50 kg max) allow to handle the cubicle by one person without any lifting provision and NR11 certification. This is reducing the certification cost for employees working with recloser control parametrization and testing. Tavrida Electric recloser control can be installed on pole by one person using a simple aerial basket car with lifting capacity of 136kg. No other recloser control with this level of internal free space not complying with this requirement.
Using Aluminium VC Stainless Steel in Circuit Reclosers Manufacturing Process
Enclosures manufactured in aluminum minimizes the energy applied to manufacturing process and leads to significant CO2 emission decreasing without any loses in quality or corrosion performance of the manufactured unit. Calculation of carbon footprint decreasing is very simples and based on the outstanding physical properties of the aluminum alloy. The density of aluminum is 2.70 g/cm3, about 1/3 that of stainless steel, much lower than other commonly encountered metals, making aluminum parts easily identifiable through their lightness. Below we get comparing analysis for aluminum and stainless steel:
Physical property | Aluminum | 304 Stainless Steel | Difference rel. |
---|---|---|---|
Density/Weight of Product | 2,70 g/cm3 | 7,93 g/cm3 | 2,94 |
Specific heat | 921 J(Kg*K) | 502,4J (Kg*K) | 0,54 |
Temperature of forming | 560 0C | 1300 0C | 2,32 |
Total | 3,69 |
CF Calculation for Transportation of Outdoor Switching Module and Recloser by Truck
Outdoor switching module and Recloser control design in aluminum ensure significant carbon footprint improvement for local transportation.
Input data for CF calculation:
- The average freight truck emits 101.5 grams of CO2 per ton-km (depends on the model and quality of the diesel);
- One 40 feet container accommodates 48 units of full assembled and packed Tavrida Electric circuit reclosers 15kV 210 kg each;
- Using aluminum in the recloser design saves 39,5 kg per one recloser 15 kV;
- 48*210 = 10.080 kg goods weight.
- 39,5*48=1896 kg weight decreased per container (truck).